Resumes
Resumes
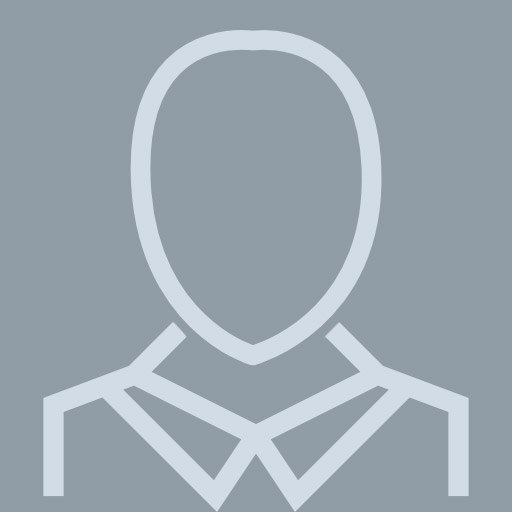
Manager Technical Services.
View pageLocation:
Knoxville, Tennessee Area
Industry:
Chemicals
Work:
Toho Tenax America, Inc. 2007 - 2010
Mgr Technical Service
GKN Aerospace 2000 - 2007
Technology Manager - M&P
Mgr Technical Service
GKN Aerospace 2000 - 2007
Technology Manager - M&P
Education:
Southern Illinois University, Carbondale 1986 - 1987
Engr
Engr