Resumes
Resumes
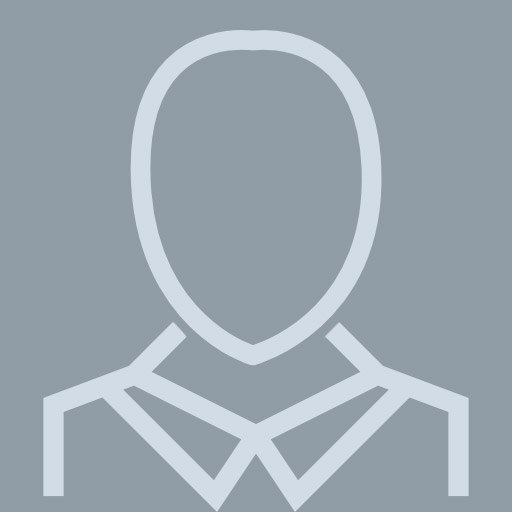
Account Representative
View pageLocation:
6459 129Th Pl southeast, Bellevue, WA 98006
Industry:
Graphic Design
Work:
Graffix
Account Representative
Account Representative
Skills:
Customer Service
Account Management
Sales Management
Leadership
Graphic Design
Digital Printing
Project Management
Sales
New Business Development
Account Management
Sales Management
Leadership
Graphic Design
Digital Printing
Project Management
Sales
New Business Development