Resumes
Resumes
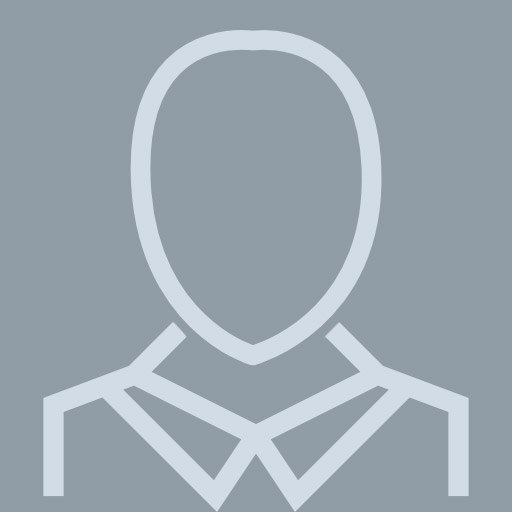
John Maltabes Austin, TX
View pageWork:
Hewlett Packard Labs
Palo Alto, CA
Apr 2009 to May 2013
Visiting Scholar
Molecular Imprints Inc
Austin, TX
Oct 2006 to Dec 2008
CMOS Applications Manager - Senior Process Engineer
Photronics Incorporated
Austin, TX
Feb 2005 to Sep 2006
Imprint Template Product Manager - Principal Engineer
Freescale Semiconductor/Motorola
Austin, TX
1993 to 2004
Principal Staff Engineer - Gold Badge
International Business Machines
Burlington, VT
1982 to 1993
Senior Associate Engineer
Palo Alto, CA
Apr 2009 to May 2013
Visiting Scholar
Molecular Imprints Inc
Austin, TX
Oct 2006 to Dec 2008
CMOS Applications Manager - Senior Process Engineer
Photronics Incorporated
Austin, TX
Feb 2005 to Sep 2006
Imprint Template Product Manager - Principal Engineer
Freescale Semiconductor/Motorola
Austin, TX
1993 to 2004
Principal Staff Engineer - Gold Badge
International Business Machines
Burlington, VT
1982 to 1993
Senior Associate Engineer
Education:
Rochester Institute of Technology
Rochester, NY
1991 to 1992
Masters in Manufacturing Engineering
Rochester Institute of Technology
Rochester, NY
1977 to 1982
BS in Science and Instrumentation
Rochester, NY
1991 to 1992
Masters in Manufacturing Engineering
Rochester Institute of Technology
Rochester, NY
1977 to 1982
BS in Science and Instrumentation