Resumes
Resumes
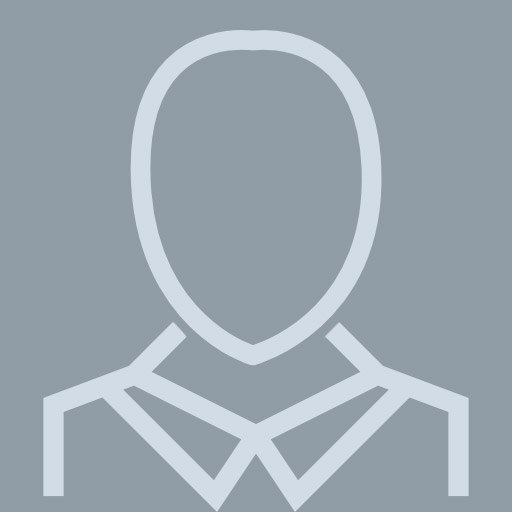
Rotor Dynamics Technical Fellow
View pageLocation:
Phoenix, AZ
Industry:
Defense & Space
Work:
Boeing
Rotor Dynamics Technical Fellow
Rotor Dynamics Technical Fellow
Skills:
Systems Engineering
Aerospace
Aerospace Engineering
Composites
Spacecraft
Finite Element Analysis
Engineering Management
Simulations
Program Management
Simulink
Structural Dynamics
Stress Analysis
Aircraft
Avionics
Space Systems
Matlab
Fortran
Aircraft Design
Flight Test
Ansys
Aeronautics
Cfd
Propulsion
Dynamics
System Design
Mil Std 1553
Trade Studies
Damage Tolerance
Systems Design
Aerospace
Aerospace Engineering
Composites
Spacecraft
Finite Element Analysis
Engineering Management
Simulations
Program Management
Simulink
Structural Dynamics
Stress Analysis
Aircraft
Avionics
Space Systems
Matlab
Fortran
Aircraft Design
Flight Test
Ansys
Aeronautics
Cfd
Propulsion
Dynamics
System Design
Mil Std 1553
Trade Studies
Damage Tolerance
Systems Design