Resumes
Resumes
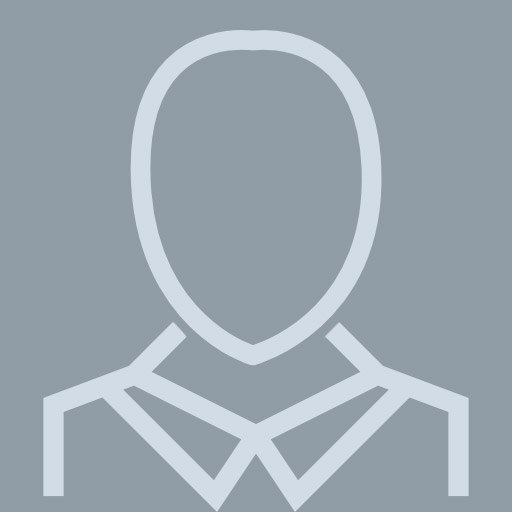
Senior Application Engineer
View pageLocation:
Palo Alto, CA
Industry:
Semiconductors
Work:
Agilone Nov 2012 - Sep 2014
Db Analyst
Mosel Vitelic Corporation Mar 2004 - Apr 2006
Staff Process Engineer
Stanford University Jan 1995 - Jan 1998
Visiting Scholar
Applied Materials Jan 1995 - Jan 1998
Senior Application Engineer
Db Analyst
Mosel Vitelic Corporation Mar 2004 - Apr 2006
Staff Process Engineer
Stanford University Jan 1995 - Jan 1998
Visiting Scholar
Applied Materials Jan 1995 - Jan 1998
Senior Application Engineer
Education:
Catholic University of America
Master of Science, Masters Epfl (École Polytechnique Fédérale De Lausanne)
Bachelors, Bachelor of Science, Physics The Catholic University of America
Master of Science, Masters, Physics Epfl (École Polytechnique Fédérale De Lausanne)
Doctorates, Doctor of Philosophy, Physics, Philosophy
Master of Science, Masters Epfl (École Polytechnique Fédérale De Lausanne)
Bachelors, Bachelor of Science, Physics The Catholic University of America
Master of Science, Masters, Physics Epfl (École Polytechnique Fédérale De Lausanne)
Doctorates, Doctor of Philosophy, Physics, Philosophy
Skills:
Semiconductors
Thin Films
Spc
Metrology
Design of Experiments
Analytics
Plasma Etch
Epitaxy
Inline Cd Sem
Thin Films
Spc
Metrology
Design of Experiments
Analytics
Plasma Etch
Epitaxy
Inline Cd Sem
Languages:
French
Turkish
Turkish
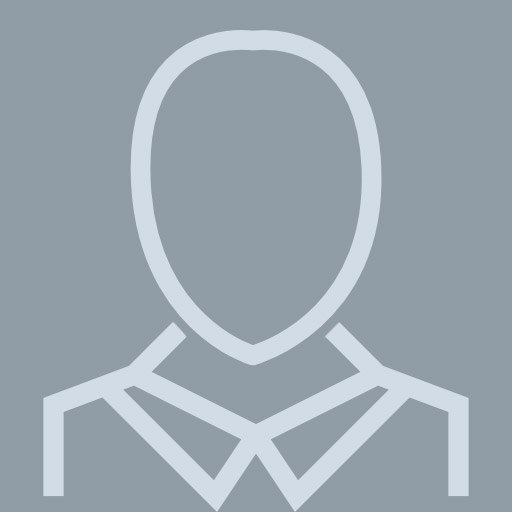
Semiconductors Professional
View pageLocation:
San Francisco Bay Area
Industry:
Semiconductors
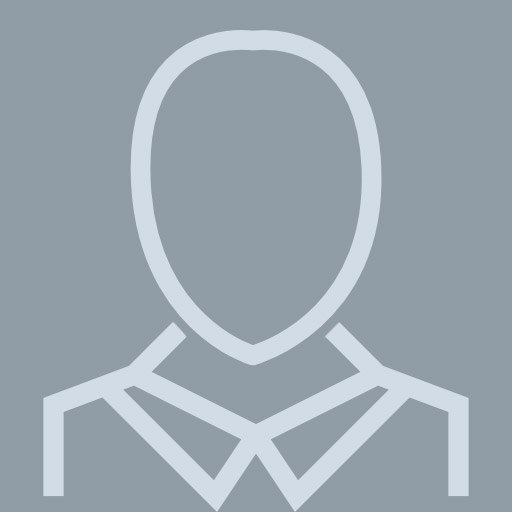
Sr. Process Eng. At Applied Materials
View pagePosition:
Sr. Process Eng. at Applied Materials
Location:
San Francisco Bay Area
Industry:
Semiconductors
Work:
Applied Materials
Sr. Process Eng.
Sr. Process Eng.