Resumes
Resumes
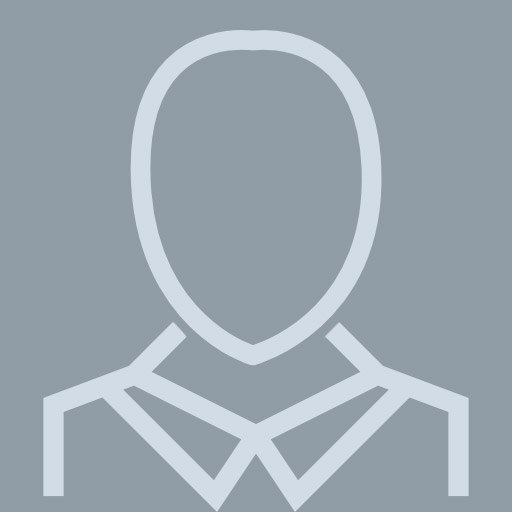
Mechanical Engineer
View pageLocation:
5630 Clay Ridge Dr, Asbury, IA 52002
Industry:
Machinery
Work:
John Deere
Mechanical Engineer
Danfoss Power Solutions May 1995 - Aug 2009
Mechanical Engineer
Mechanical Engineer
Danfoss Power Solutions May 1995 - Aug 2009
Mechanical Engineer
Education:
Iowa State University 1997 - 2003
Masters, Mechanical Engineering Iowa State University 1989 - 1995
Bachelors, Bachelor of Science, Mechanical Engineering, Agricultural Engineering
Masters, Mechanical Engineering Iowa State University 1989 - 1995
Bachelors, Bachelor of Science, Mechanical Engineering, Agricultural Engineering
Skills:
Fluid Power
Matlab
Dynamic Systems Modeling
Matlab
Dynamic Systems Modeling
Certifications:
License 8N3Dhmhchy
License 3Xm699G6Ch
License X2Wf2Xaymw
Coursera Verified Certificates, License 8N3Dhmhchy
Coursera Verified Certificates, License 3Xm699G6Ch
Coursera Verified Certificates, License X2Wf2Xaymw
Fundamentals of Fluid Power
Linear Circuits
Introduction To Programming With Matlab
License 3Xm699G6Ch
License X2Wf2Xaymw
Coursera Verified Certificates, License 8N3Dhmhchy
Coursera Verified Certificates, License 3Xm699G6Ch
Coursera Verified Certificates, License X2Wf2Xaymw
Fundamentals of Fluid Power
Linear Circuits
Introduction To Programming With Matlab