Resumes
Resumes
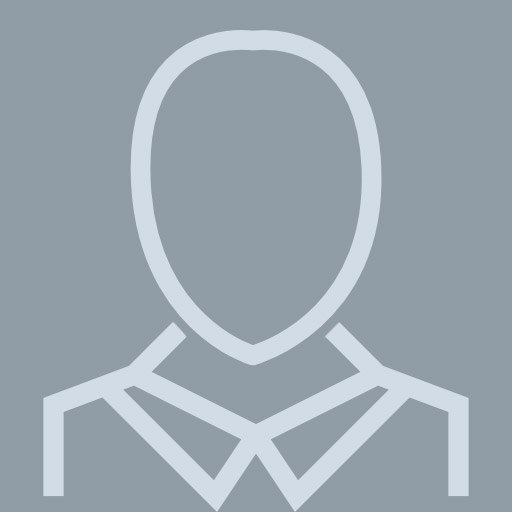
Engineering Fellow
View pageLocation:
Danville, KY
Industry:
Glass, Ceramics, & Concrete
Work:
Corning Incorporated
Engineering Fellow
Corning Incorporated
Technology Manager, Senior Engineering Assoc
Engineering Fellow
Corning Incorporated
Technology Manager, Senior Engineering Assoc
Education:
Massachusetts Institute of Technology 1973 - 1977
Bachelors, Bachelor of Science
Bachelors, Bachelor of Science