Resumes
Resumes
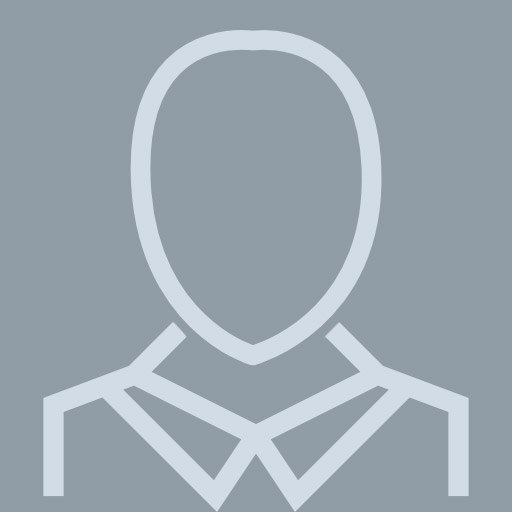
Engineer
View pageLocation:
Boston, MA
Industry:
Computer Hardware
Work:
Finish Line Pds
Engineer
Stratasys Oct 1997 - Mar 2017
Principal Engineer
Stratasys Jan 2015 - Mar 2017
Principal Engineer at Skunkworks 1
Solidscape, Inc. Oct 1997 - Dec 2015
Principle Engineer
Howtek 1985 - Oct 1997
Engineer
Engineer
Stratasys Oct 1997 - Mar 2017
Principal Engineer
Stratasys Jan 2015 - Mar 2017
Principal Engineer at Skunkworks 1
Solidscape, Inc. Oct 1997 - Dec 2015
Principle Engineer
Howtek 1985 - Oct 1997
Engineer
Education:
Massachusetts Institute of Technology 1980 - 1981
Master of Science, Masters, Mechanical Engineering Massachusetts Institute of Technology 1976 - 1980
Bachelors, Bachelor of Science, Microbiology, Mechanical Engineering
Master of Science, Masters, Mechanical Engineering Massachusetts Institute of Technology 1976 - 1980
Bachelors, Bachelor of Science, Microbiology, Mechanical Engineering
Skills:
R&D
Inkjet
Engineering Management
Product Design
Electronics
Manufacturing
Product Development
Root Cause Analysis
C++
Sql
Image Processing
Automated Product Testing
Mechanical Engineering
Quality System
Design of Experiments
Automation
Embedded Systems
Design For Manufacturing
Inkjet
Engineering Management
Product Design
Electronics
Manufacturing
Product Development
Root Cause Analysis
C++
Sql
Image Processing
Automated Product Testing
Mechanical Engineering
Quality System
Design of Experiments
Automation
Embedded Systems
Design For Manufacturing