Resumes
Resumes
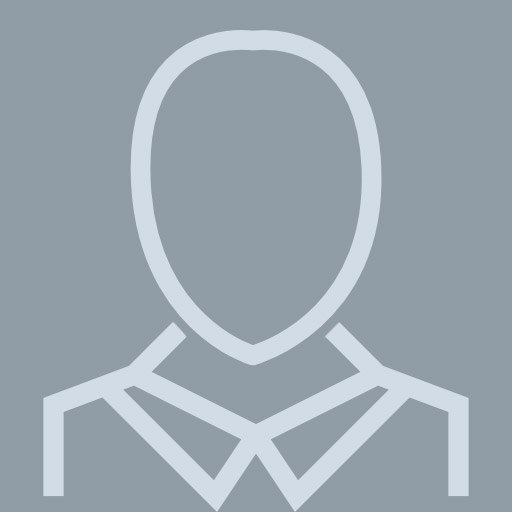
Senior Technical Manager
View pageLocation:
Phoenix, AZ
Industry:
Aviation & Aerospace
Work:
Honeywell Apr 1996 - Jun 2006
Principal Engineer
Honeywell Apr 1996 - Jun 2006
Senior Technical Manager
Pratt & Whitney Canada Apr 1990 - Apr 1996
Principal Engineer
Bc Research Centre Feb 1988 - Nov 1989
Consultant Engineer
Principal Engineer
Honeywell Apr 1996 - Jun 2006
Senior Technical Manager
Pratt & Whitney Canada Apr 1990 - Apr 1996
Principal Engineer
Bc Research Centre Feb 1988 - Nov 1989
Consultant Engineer
Education:
The University of British Columbia 1983 - 1990
Doctorates, Doctor of Philosophy, Philosophy, Mechanical Engineering The University of British Columbia 1983 - 1985
Masters, Mechanical Engineering Chatrapati Sahuji Maharaj Kanpur University, Kanpur 1980 - 1983
Bachelors, Bachelor of Science, Mechanical Engineering
Doctorates, Doctor of Philosophy, Philosophy, Mechanical Engineering The University of British Columbia 1983 - 1985
Masters, Mechanical Engineering Chatrapati Sahuji Maharaj Kanpur University, Kanpur 1980 - 1983
Bachelors, Bachelor of Science, Mechanical Engineering
Skills:
Aerospace
Engineering
Engineering Management
Mechanical Engineering
Aerospace Engineering
Finite Element Analysis
Six Sigma
Systems Engineering
Ansys
Matlab
Continuous Improvement
Manufacturing
Engineering
Engineering Management
Mechanical Engineering
Aerospace Engineering
Finite Element Analysis
Six Sigma
Systems Engineering
Ansys
Matlab
Continuous Improvement
Manufacturing
Languages:
English
Farsi
Farsi