Resumes
Resumes
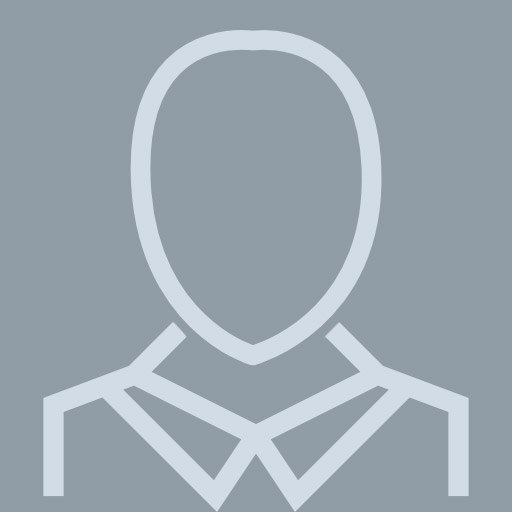
Alexander Brown Dayton, NJ
View pageWork:
Green, Lundgren & Ryan, P.C
Aug 2012 to Dec 2012
Law Clerk
Professor Author Laby
Camden, NJ
May 2012 to Dec 2012
Research Assistant
NEW JERSEY ATTORNEY GENERAL'S OFFICE, DIVISION OF LAW
Trenton, NJ
May 2012 to Aug 2012
Intern
HON. THEODORE MCKEE, CHIEF JUDGE, U.S. COURT OF Appeals, THIRD CIRCUIT
Philadelphia, PA
Jan 2012 to Apr 2012
Judicial Intern
HON. THOMAS N. O'Neill
Philadelphia, PA
May 2011 to Aug 2011
Judicial Intern
MUSIC CHOICE, INC
New York, NY
Oct 2008 to Dec 2009
Music Programming Assistant
Aug 2012 to Dec 2012
Law Clerk
Professor Author Laby
Camden, NJ
May 2012 to Dec 2012
Research Assistant
NEW JERSEY ATTORNEY GENERAL'S OFFICE, DIVISION OF LAW
Trenton, NJ
May 2012 to Aug 2012
Intern
HON. THEODORE MCKEE, CHIEF JUDGE, U.S. COURT OF Appeals, THIRD CIRCUIT
Philadelphia, PA
Jan 2012 to Apr 2012
Judicial Intern
HON. THOMAS N. O'Neill
Philadelphia, PA
May 2011 to Aug 2011
Judicial Intern
MUSIC CHOICE, INC
New York, NY
Oct 2008 to Dec 2009
Music Programming Assistant
Education:
RUTGERS SCHOOL OF LAW
Camden, NJ
2013
Juris Doctor, magna cum laude
Camden, NJ
2013
Juris Doctor, magna cum laude